Metal Finishing Processes
The metal finishing process is a very dynamic process.
Click on each process below for more information.
Electroplating
The uses of electroplated articles can be decorative or functional. Both uses require some degree of corrosion resistance; however, corrosion resistance is more critical when electroplating for functional uses. Metals and alloy substrates account for much of the volume in electroplating, although there is a large and growing amount of plastic surfaces being plated, both for decorative trim and for electronic shielding applications. Other materials that may be plated include:
- Wood
- Plaster
- Fibers and cloth materials
- Plant and animal tissues, such as leaves, leather, paper, and seashells
Anodizing
Anodizing is an electrochemical process whereby stable films or coatings (insoluble oxides) are formed on the surface of metals. Aluminum is commonly anodized using an electrolyte (chromic, sulfuric, or boric acid) and either alternating or direct current. The anodic oxide coating is resistant to corrosion.
Electroforming
Electroforming is an adaptation of the electroplating process. Electroforming involves plating a mold, or mandrel, with metal, removing the plated form from the mold, and using the resulting plated form. Mandrels can be either reusable or disposable, depending on the complexity of the shape. Electroforming is used to make very thin copper sheets for use in electronic circuit boards.
Electroless Plating
Electroless plating involves the deposition of metal onto the article to be plated simply by immersing the article in a solution. The electrons are supplied by a chemical reducing agent dissolved in the solution rather than a direct electric current source.
Electroless deposition is defined as the auto-catalytic chemical reduction of metal from solution. Thus, the metal depositing on a suitable surface is catalytic for the chemical reduction process, and deposition proceeds solely on this surface. Metals that can be plated using this process include:
- Nickel
- Cobalt
- Copper
- Palladium
Conversion Coating
Conversion coating is a process by which a thin film of chromate or metal phosphate is applied to electroplated or metal surfaces to improve corrosion resistance, or to prepare the metal surface for painting. Included in this process are metal coloring and passivating.
Chromate Conversion Coating
Chromate conversion coating is most commonly applied to zinc plated articles; however, many electroplated metals other than zinc can be chromate coated. The chromate coating is formed by a chemical reaction between the metal surface and hexavalent chromium in solution. The metal surface may need to be anodized for certain types of chromate conversion baths. The chemical reaction is a controlled oxidation-reduction reaction in which the metal is oxidized by the hexavalent chromium, which is reduced to trivalent state.
When the reaction occurs, the pH at the metal-liquid interface rises, which causes the trivalent chromium compounds to precipitate on the surface, forming a gelatinous film. This film buildup on the metal surface entraps some soluble hexavalent chromium. The color of the film is controlled by the concentration of hexavalent chromium in the conversion coating bath. Chromate-conversion coating solutions are usually acidic and contain hexavalent chromium and dissolved metals. Conversion coating adds several rinsing steps (before and after plating and conversion coating) and the actual conversion coating step to the electroplating process.
Galvanizing
Galvanizing is the application of a thin zinc coating to a ferrous surface. The zinc coating may be applied by either the hot-dip method, where ferrous metal is passed through a bath of molten zinc, or by the electrodeposition method.
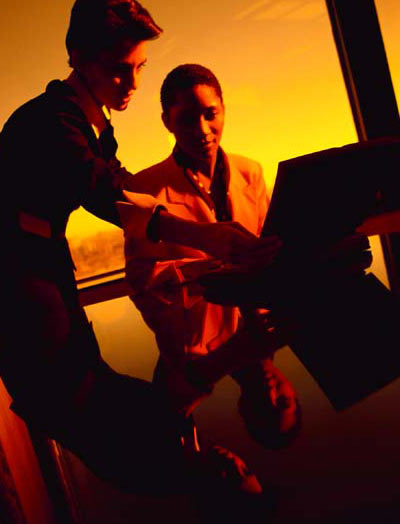
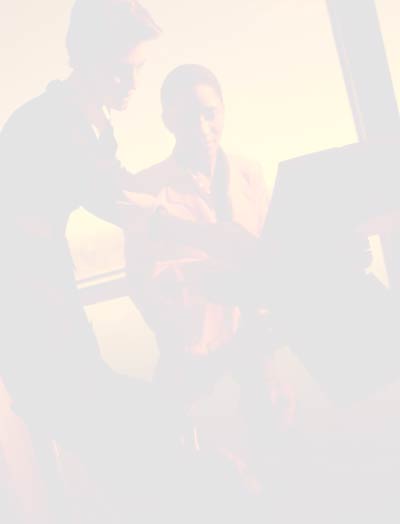